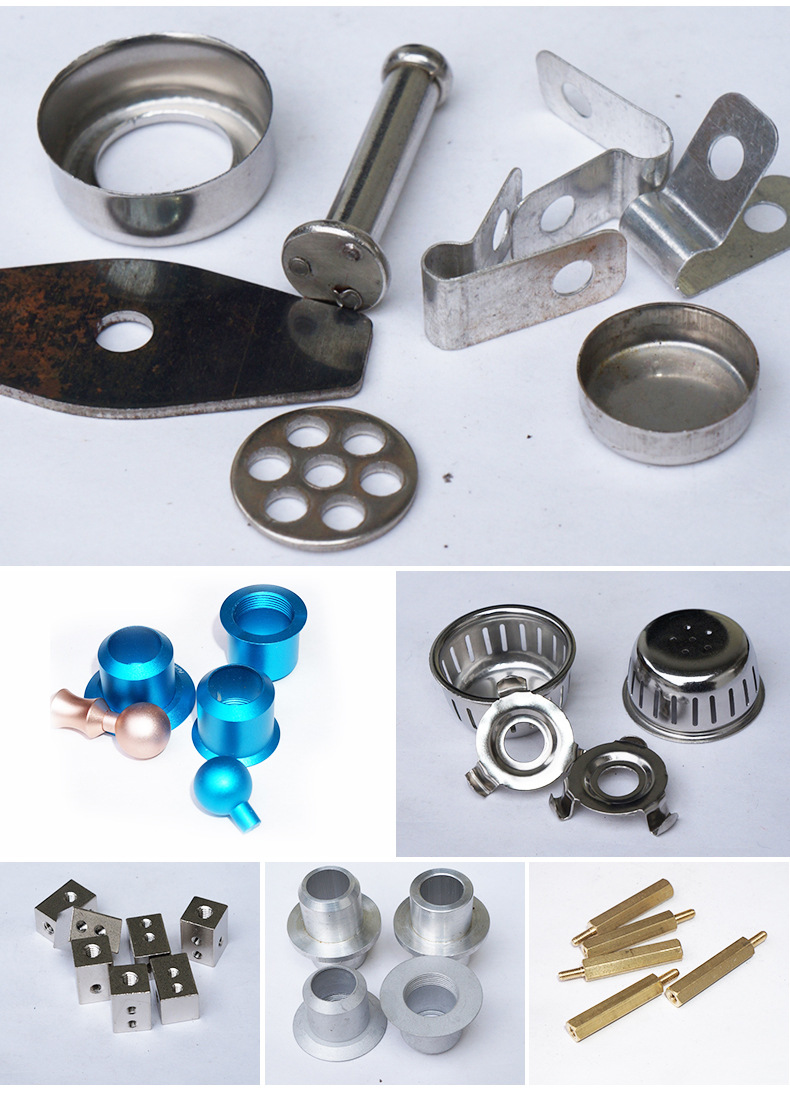
非标零部件通常是根据特定需求定制的,其质量直接关系到最终产品的性能和安全性。质量检测在非标零部件加工中起着至关重要的作用。
首先,通过质量检测可以确保非标零部件符合设计要求。在加工过程中,由于各种因素的影响,零部件可能会出现尺寸偏差、形状不规则等问题。质量检测能够及时发现这些问题,并采取相应的措施进行调整,确保零部件的尺寸精度和形状精度符合设计标准。
其次,质量检测有助于提高产品的性能和可靠性。非标零部件往往在复杂的工作环境中运行,对其性能和可靠性要求较高。通过对零部件的材料性能、机械性能、表面质量等进行检测,可以确保其具备足够的强度、硬度、耐磨性、耐腐蚀性等性能,从而提高产品的整体性能和可靠性。
此外,质量检测还可以保障产品的安全性。在一些关键领域,如航空航天、汽车制造、医疗器械等,非标零部件的质量直接关系到人员的生命安全。严格的质量检测可以排除存在安全隐患的零部件,降低事故发生的风险。
据统计,在汽车制造行业中,由于零部件质量问题导致的事故占比高达 30%。这充分说明了非标零部件加工质量检测的重要性。只有通过严格的质量检测,才能确保非标零部件的质量,从而为产品的性能和安全性提供有力保障。
二、常见的非标零部件质量检测方法
(一)电子档校核
在非标零部件加工质量检测中,电子档校核是重要的一环。首先,我们根据相应编码查询图档,打开文件包后对所有项目逐一查看。对于本次实例中的大钣金件,需重点查看 ECN 更改记录,包括备注和更换设备项等。通过电子档校核,可以确保设计文件的准确性和完整性,为后续的加工和检测提供可靠的依据。
(二)对照纸质图纸检验
纸质图纸是零件制造过程中的参照标准。在检验时,需查看总体装配图,确保各个部件的位置和连接关系正确。校核组件图、部件图和焊接图,检查焊接质量和部件的配合精度。同时,校核零件图,确保零件的尺寸和形状符合要求。最后进行整体零部件校对,保证整个产品的装配精度。
(三)3D 模型校对
零部件存放时应按照要求归档。对非标零部件进行重点检查,尤其是重要尺寸。明确技术要求,对重要参数进行校核。利用 3D 模型可以更加直观地观察零部件的形状和结构,发现潜在的问题,提高检测的准确性和效率。
(四)防水检验
防水检验对于非标零部件尤其是机柜等设备至关重要。第一步是对机柜的密封性进行检验,特别是涂胶处,要严格按照标准进行查看。同时,要解决户外漏水问题,对防水检验进行重点监控,参照标准指导检验工作。例如,在汽车各零部件标准中,对 IPX9K/IP69K 防水试验有严格要求,不同汽车公司的企业标准在国际标准基础上进行改进,如德国大众汽车公司对汽车电器电子产品的通用试验要求中对防水试验的要求引用自德 DIN40050 - 9 标准中的 IPX9K 的基本要求,并对测试水温、喷水位置等进行调整。
(五)常规性检验
- 成批对比检验:对批量生产的非标零部件进行对比检验,确保产品的一致性。
- 整体外观检验:检查零部件的表面光洁度、无色差、无划痕、污迹、毛刺等。
- 标签检验:检查标签的完整性和准确性,便于生产识别和后续追踪。
(六)验后处理
产品检验合格之后,加上过审标签。过审标签可以为生产过程中的识别提供便利,同时也方便后续的质量追踪和管理。通过验后处理,可以确保产品的质量可追溯,提高生产管理的效率和质量控制水平。
三、质量鉴定的方式与步骤
(一)要素检验法
在质量要求条款约定不明确又无法达成补充协议时,对非标设备应采取 “要素检验法”,通过设备样品特性、生产效率要求、最长使用年限、调试维修次数等合同要素,确定是否符合 “合同目的特定标准”。例如在一个机械加工的非标零部件案例中,合同约定了零部件的生产效率应达到每小时加工一定数量的特定零件。在质量鉴定时,就需要重点考察实际生产效率是否符合合同约定。同时,对于最长使用年限的考量,可以通过对零部件材料的耐久性分析以及类似产品的使用经验来判断。如果合同中规定了调试维修次数不能超过一定范围,那么在鉴定过程中,需要统计实际的调试维修情况,以此综合判断非标零部件是否符合质量要求。
(二)全面质量鉴定步骤
- 制定鉴定标准和测试方法,确保鉴定的客观性和准确性。在制定标准时,要充分考虑非标零部件的特殊用途和使用环境。比如对于在高温、高压环境下使用的非标零部件,鉴定标准应包括耐高温、耐高压的性能指标。测试方法可以采用专业的检测设备和仪器,如硬度测试仪、金相分析仪等,确保测试结果的准确性。
- 进行外观检查和功能测试。外观检查主要检查零部件的表面是否有划痕、裂纹、变形等缺陷。功能测试则是验证零部件是否能够正常实现其设计功能。例如,对于一个非标齿轮,要检查其齿形是否完整,啮合是否顺畅,传动是否稳定。
- 进行性能测试,包括耐久性、稳定性、安全性等方面的测试,以确保设备在长期使用中的可靠性。耐久性测试可以通过模拟实际使用环境,进行长时间的运行测试,观察零部件的磨损情况和性能变化。稳定性测试可以通过对零部件施加一定的负荷,观察其在不同工况下的性能表现。安全性测试则是检查零部件是否存在安全隐患,如是否会发生断裂、爆炸等危险情况。
- 进行实际应用测试,将设备放入实际工作环境中进行测试,评估其适应性和性能。实际应用测试可以让我们更直观地了解非标零部件在实际使用中的表现,发现潜在的问题。例如,将非标零部件安装在实际的机械设备中,观察其与其他部件的配合情况,以及对整个设备性能的影响。
- 对检测结果进行分析和评估,提出改进意见和建议,为设备的完善和优化提供参考依据。在分析检测结果时,要结合非标零部件的设计要求和使用环境,综合考虑各项指标的重要性。对于不符合质量要求的项目,要提出具体的改进措施,如调整加工工艺、更换材料等。同时,要对整个质量鉴定过程进行总结,为今后的质量鉴定工作提供经验参考。
四、检验要点与规范
(一)零部件检验规范
全检项包括所有的非标零部件,抽检项为采购的批量标准件或批量生产的零件,按 20% 的比例抽样。品管部在检验过程中,对发现的不良品不接受、不流转,并记录相关数据向生产部门及采购部门反馈问题。同时,统计和分析不良原因并跟踪改善。
检验依据包括公司审核图纸中的尺寸及技术要求,以及依据 GB 控制自由公差要求。在检验过程中,首先要确定图纸中重要尺寸,确认零件是否加工完成且达到图纸要求的几何形状。若检验过程中发现超差,检验员在不确定的情况下,可向组长反映情况,由技术部来判定,按不合格品控制程序来处理。
检验项目涵盖检具上的底板、型面、定位、铝柱、标准件、车磨件销子、库房备用标准件等。例如底板检验规范,外观要求被测表面无飞刀痕、裂纹、砂眼、针孔等;图纸上要求的孔需用通止规、游标卡尺进行孔径检验;平行度及平面度要求被测表面放至在大理石平台上,误差在 0.03 内;刻字大小及方向需参照刻字要求,刻线宽度 0.8,深度 0.5。
(二)质量标准及检验规范
- 作业前检验要求:板材中间严重分层开裂,凹凸不平,粘压移位等板件不可投入本工序生产;贴皮板面起皱,严重刮伤,开皮,木纹方向不正确板件不可投入本工序生产;刀具不够锋利、损坏缺茬等不能投入本工序生产。
- 立铣、铣型质量标准:
- MDF 材质・立铣:各种压线、形状符合工艺图纸和有关技术参数的规定。所有加工面要求平整、顺畅、光滑、转角自然、弧度一致、线条流畅、手摸无起伏坑凹、波浪、刀痕、台阶、缺茬。要求加工无焦黑,无严重起毛、崩裂、加工面无损坏板面现象。产品必须写有正确单号,字迹工整清晰。
- 实木材质・铣型:活节 Φ<1CM 允许、死节不允许。肯头、缺茬、焦黑、起毛、崩裂、刀痕、台阶不允许。尺寸错误不允许。产品必须写有正确单号,字迹工整清晰。
- 各种包类:铣型形状符合工艺图纸和有关技术参数的规定。波浪、缺茬、变形、肯头、凹坑不允许。加工面允许少量小于 0.2 的跳刀痕(打磨掉,不影响造型美观及尺寸允许)。包尺寸宽大于 200mm 长大于 1000mm 时,允许公差为 ±1mm(长度)、±0.5mm(厚度)。产品必须写有正确单号,字迹工整清晰。
- 玻璃芯类:加工面允许少量小于 0.2 的跳刀狠、波浪纹(容易打磨掉,不影响造型美观及尺寸允许)。雕刻形状符合工艺图纸和有关技术参数的规定。崩边、缺茬、缺皮不允许,尺寸雕刻错误不允许。产品必须写有正确单号,字迹工整清晰。
- 帽头类、制作质量标准:各种造型、尺寸符合工艺图纸要求。造型做错、尺寸做错不允许。帽板开料尺寸公差为长 ±1mm、宽 ±1mm。组装对接缝隙公差 0.3mm 以下允许。帽板、帽线起泡、缺皮、夹皮、开皮、透胶、起皱、杂质、拔缝、二层皮不允许。帽板变形翘曲度公差根据长度不同有所区别,长 1000mm 以内允许 0.5mm;长 1000mm~2000mm 允许 2mm;长超出 2000mm 时,每加长 1000mm 翘曲度公差同时加 1mm 允许。
五、加工注意事项与材料要求
(一)加工注意事项
- 研磨注意事项:非标零件加工需要注意研磨用磨料粒度应由粗到细,顺次更换。在更换磨料时,应将前道工序的磨削痕迹完全除去,研磨要进行到只能看见本次磨削痕迹为止,这对于防止出现 “浮雕” 现象是非常重要的。同一研具只能使用同一粒度的磨料,每次改换粒度之前,必须将工件彻底清理一遍,以不使较粗的磨粒或其他污物带到下一工序,造成研磨表面的划伤。每次往下一粒度转换的时候,要和上一次磨削方向成 30 - 45° 角进行磨削。若有很深的伤痕时,不能只对此局部位置进行研磨,否则会使此局部位置现凹坑,要进行全面修整,除去凹坑。对容易研磨与不容易研磨的站位都需要注意进行均匀的研磨。
- 防止工件变形注意事项:
- 工件的材料和结构影响:变形与形状复杂性、纵横比和壁厚以及材料的刚度和稳定性成正比。在零件设计中,应尽量减少这些因素对工件变形的影响。尤其是大型零件的结构要合理,加工前应严格控制毛坯的硬度、气孔等缺陷,以保证毛坯质量,减少工件变形。
- 工件装夹引起的变形:夹持工件时,应先选择正确的夹持点,再根据夹持点的位置选择合适的夹持力。夹持点和支撑点应尽量保持一致,使夹持力作用在支撑上。装夹点应尽量靠近加工面,应选择受力不易引起装夹变形的位置。当工件上作用有多个夹紧力方向时,应考虑夹紧力的顺序。工件与支架接触时,夹紧力应先作用,不易过大。对于平衡切削力的主夹紧力,应最后作用。其次,应增加工件与夹具的接触面积或使用轴向夹紧力。例如,铣削薄壁零件时,大量使用弹性压板,以增加接触零件的受力面积;在车削薄壁套筒的内径和外圆时,使用简单的开口过渡环、弹性芯轴、整体弧形爪等,都是为了增加接触面积。轴向夹紧力在生产中也被广泛使用,专用夹具的设计制造,可使夹持力作用于端面,解决因工件壁薄、刚性差而造成的工件弯曲变形。
- 工件加工引起的变形:在切削过程中,由于切削力的作用,工件在力的方向上产生弹性变形。针对这种变形,应对刀具采取相应的措施。精加工时,要求刀具锋利,一方面可以减小刀具与工件摩擦形成的阻力,另一方面可以提高刀具切削工件时的散热能力,从而减少内部残留工件上的应力。例如,铣削薄壁零件的大平面时,采用单刃铣法,刀具参数选择较大的主偏角和较大的前角,以降低切削阻力。在薄壁零件车削中,合理的刀具角度对切削力、热变形和工件表面的微观质量都非常重要。正确选择刀具是处理工件变形的必要条件。在加工中,刀具与工件摩擦产生的热量也会使工件变形,因此常选择高速加工。在高速加工中,由于排屑时间短,切削热大部分被切屑带走,减少了工件的热变形;其次,在高速加工中,切削层材料软化部分的减少也可以减少零件的变形,有利于保证零件的尺寸和形状精度。此外,合理使用切削液对提高刀具寿命、加工表面质量和加工精度具有重要作用。合理选择切削参数是保证零件精度的关键因素。在加工精度要求较高的薄壁零件时,一般采用对称加工,使相对两侧产生的应力平衡,达到稳定状态。加工后工件光滑。但是,当某道工序需要较大的切削量时,由于拉应力和压应力的不平衡,工件就会发生变形。
(二)材料要求
- 对材料硬度的要求:在某些情况下,硬度越高材料越好,但对于精密机械零部件加工来说,材料只能局限于车床车刀的硬度,如果材料比车床车刀还要硬,那就无法进行加工。
- 材料应软硬适中:精密机械零部件加工材料至少要比车床车刀的硬度低。同时,要了解精密机械零部件的用途是什么,从而选择合适的车床车刀进行加工。
- 应注意材料的密度:在进行精密机械零部件加工前一定要注意材料的密度,如果密度过大,相当于硬度也很大,但硬度超过车床车刀的硬度,就无法进行加工的,不仅会损坏的车床车刀,还会造成车刀断飞等危险。总之,在进行精密机械零部件加工时,加工材料硬度要低于车床车刀的硬度才能进行精密机械加工。
六、加工标准与电气部分检验
(一)机械部分加工标准
以气缸为例,气缸直径一般不小于 20MM,除特殊场合。对于气缸的尺寸要求非常严格,例如嵌入式气缸的直径,正负误差必须在合格零件范围内,否则视为不合格。如果直径太大并超过允许误差范围,会导致实际直径太小并超出误差允许负值的下限,从而出现插入太松、不稳定的问题。同时,气缸长度也有严格要求,太长或太短,超出允许误差,都是不合格产品。
在基本装配部分,零件在装配前必须清理和清洗干净,不得有毛刺、飞边、氧化皮、锈蚀、切屑、砂粒、灰尘和油污等。装配过程中零件不得磕碰、划伤和锈蚀。相对运动的零件,装配时接触面间应加润滑油(脂)。各零、部件装配后相对位置应准确。装配时原则上不允许踩机操作,特殊部位必须上机操作时应采取特殊措施,应用防护罩盖住被踩部位,非金属等强度较低部位严禁踩踏。螺钉、螺栓和螺母紧固时严禁打击或使用不合适的板手,紧固后螺钉槽、螺母、螺钉及螺栓头部不得损伤。同一零件用多个螺钉或螺栓紧固时,各螺钉(螺栓)需顺时针、交错、对称逐步拧紧,如有定位销,应从靠近定位销的螺钉或螺栓开始。螺钉、螺栓和螺母拧紧后,其支承面应与被紧固零件贴合。平键与固定键的键槽两侧面应均匀接触,其配合面间不得有间隙。
在轴承装配方面,轴承在装配前必须是清洁的。装配时应用专用套筒顶住轴承内圈(外圈),用铜棒敲击套筒,将轴承装到轴(座)上所需位置。将轴承往轴上安装时,外力应作用在内圈上,将轴承往座孔内装时,外力应作用在外圈上,轴承带编号或油封一侧朝外。滚动轴承装好后,相对运动件的转动应灵活、轻便,不得有卡滞现象。装配前先在轴承与轴、轴承与座的配合面上涂抹少量润滑油。
(二)电气部分检验
- 操作面板检验标准:
- 操作面板位置合适,便于操作。
- 指示灯(塔灯)设置齐全,不同功能的指示灯设置不同颜色,绿色(电源)、黄色(状态)、红色(故障)。
- 按键开关设置齐全,能够单独运动的模块,需要有相应的手动开关。
- 急停按钮,连接常闭点。
- 面板所有能被操作的按钮、开关要有明确的指示标牌,并固定。
- 面板需要有固定的存放保护位置,面板的引线要牢固可靠且留有操作余量。
- 操作台应布置合理,便于维修、更换。
- 移动式操作台必须内置单独接地。
- 有其他环境要求的操作台需要做好防尘防水等密封措施。
- 其他环境要求的操作台检验标准:
- 对于有防尘防水等密封要求的操作台,必须确保密封措施到位,防止灰尘、水气、油污等进入操作台内部,影响设备的正常运行。
- 对灰尘、水气、油污比较大的环境,操作台箱体要有良好的密封设施,如采用密封胶条、密封垫等进行密封。同时,箱体结构及四周空间大小要便于维修,方便操作人员进行维护和检修。
- 在操作台上安装的各种元件,如按钮、开关、指示灯等,应固定牢固,并有明确的名称指示标牌,便于操作人员识别和操作。
- 操作台上的电线引线要可靠固定,并在打开过程中移动部位留有一定长度的余量,以防止电线因拉扯而损坏。
- 对于可移动式操作台,除了内置单独接地外,还应考虑其在移动过程中的稳定性和安全性,防止因操作不当而导致设备损坏或人员受伤。
七、总结与展望
非标零部件加工质量检测标准在现代制造业中起着至关重要的作用。它不仅确保了非标零部件的质量符合设计要求,提高了产品的性能和可靠性,还保障了产品的安全性,降低了事故发生的风险。
然而,非标零部件加工质量检测也面临着一些挑战。一方面,随着科技的不断进步,非标零部件的种类和复杂性不断增加,对质量检测技术和方法提出了更高的要求。例如,新型材料的应用、精密加工技术的发展以及自动化技术的普及,都需要相应的质量检测手段来保证零部件的质量。另一方面,成本压力也是一个重要的挑战。质量检测需要投入大量的人力、物力和财力,这对于企业来说是一笔不小的开支。如何在保证质量检测效果的前提下,降低检测成本,是企业需要思考的问题。
尽管面临着挑战,但非标零部件加工质量检测的发展前景依然广阔。随着工业 4.0 的推进和智能制造的发展,质量检测技术将不断创新和完善。物联网技术、数据分析与人工智能、远程监控与维护等先进技术的应用,将大大提高质量检测的效率和准确性,实现智能化检测。同时,随着市场对产品质量要求的不断提高,企业对质量检测的重视程度也将不断增加,这将为质量检测行业带来更多的发展机遇。
总之,非标零部件加工质量检测标准是保证产品质量的重要手段,虽然面临着挑战,但发展前景广阔。我们相信,在科技的不断推动下,非标零部件加工质量检测技术将不断创新和完善,为制造业的发展做出更大的贡献。